2021.02.22
グローバル製造業における原価管理の高度化
迅速かつ的確な意思決定を支える生きた原価情報とは
髙山 直子
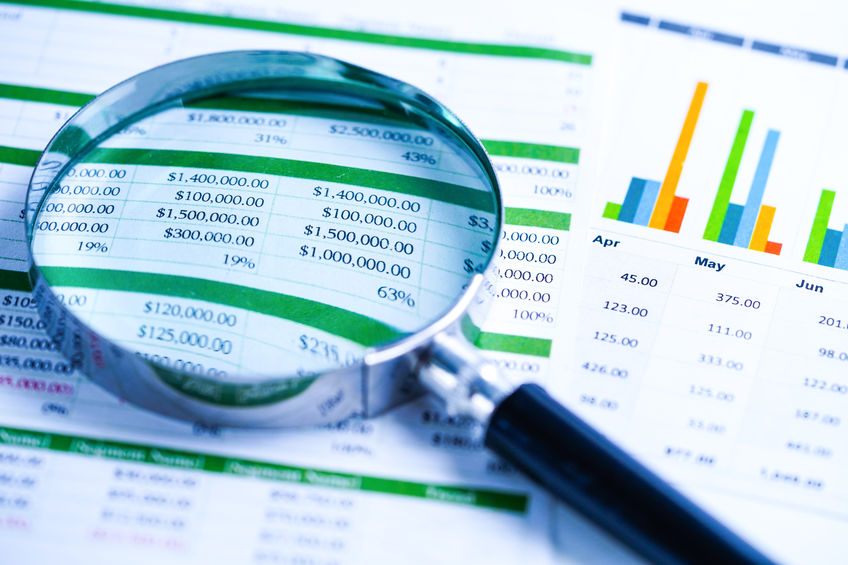
「自動車メーカーがコスト管理によって逆風下でも利益を増加」―そんな新聞記事やネットニュースを目にすることがある。本稿のテーマである原価管理は、マーケティングや新規事業開発といったテーマに比べて、売上拡大に直結する革新的な取り組みではないため後ろ向きに捉えられることもあるが、市場の影響を受けず社内の力で強化し、結果を出すことができる意義の大きい取り組みである。米中貿易摩擦、新型コロナウイルス感染症の拡大、各社のDX推進加速など、企業を取り巻く環境変化のスピードや不透明感が増す中、改めて原価管理の高度化を図る企業が増えている。
ここでいう原価管理とは、単にコストの低減活動を意味しているのではない。グローバルに展開する販売拠点や工場を統括しながら、精度の高い生きた原価情報を管理統制し、利益拡大や資本効率向上に向けた最適な意思決定に活用する、そんなグローバル経営管理に必要不可欠な原価管理の仕組みづくりについて解説する。
制度会計ではなく管理会計による原価情報が必要
原価計算は、制度会計と管理会計の2つを目的に行われている。
制度会計では、各企業は共通の会計ルールに則り、四半期、年度で財務情報を開示して会計責任を果たすために原価を計算する。一般的に、制度会計の原価情報は、全社・対外的なセグメント別と情報の単位が大きく、財務情報が中心で、正確性が求められるために算出に時間がかかる。また、実績に着目することから将来的予測には使いづらいという特徴をもち、意思決定のための情報としては十分ではない。そこで、各企業は販売や生産などの財務以外の情報と組み合わせて、独自のルールや仕組みをもって必要な原価情報を捉え、内部管理用の会計データとして分析している。いわゆる管理会計である。しかし、この独自ルールや仕組みの構築が簡単ではなく、企業によって差が生じているのが実態である。
自社にとって、各種意思決定にどのような情報が必要か。原価管理の高度化は、原価情報の要件を明確にすることから始まる。
意思決定に必要な原価情報は企業によって異なる
原価情報が必要となる意思決定は、具体的に以下のような種類がある。
①経営的意思決定(事業ポートフォリオの最適化やそれに基づく事業や工場への投資判断、組織再編など)
②利益計画(目標利益を確保する販売・生産・在庫計画の立案や予算設定など)
③売価設定(新製品の値決めや既存製品の価格改定、値引き交渉への対応など)
④原価統制(開発・設計・調達・製造における原価低減活動など)
これら意思決定の種類によって必要となる原価情報は異なるが、たとえ同じ種類の意思決定であっても、企業によって使用する原価情報は異なる。求められる原価情報のサイクル(タイミング)、単位(切り口)、粒度(値の細かさ)は、各企業の業種、製品を投入している市場の状況、製品特性、生産形態、組織構造などによっても異なるからである。また、組み合わせにより、標準原価(見積原価)、実績原価、実際原価[1]のどれを使用すべきかも変わってくる。
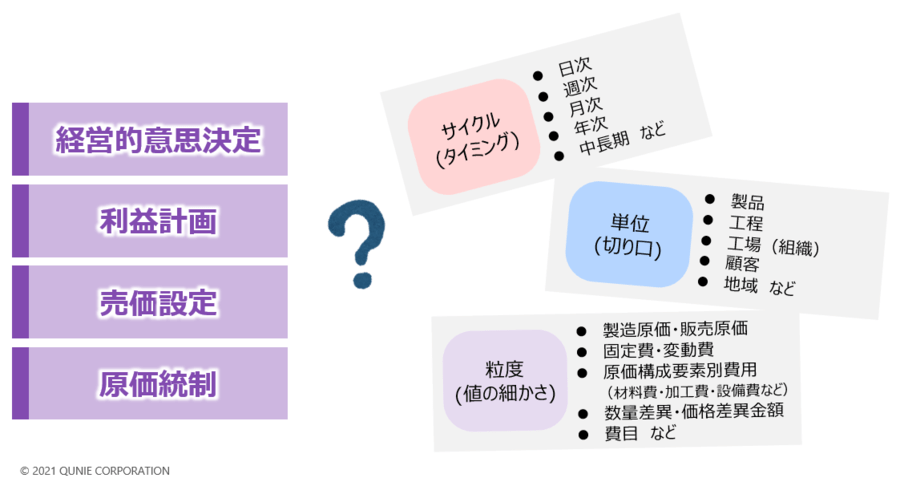
意思決定の種類と原価情報の要件
例えば、目標利益の確保に向けて販売計画や生産計画を調整していく意思決定において、製品ライフサイクルの短い電機メーカーの場合、減産や製造切替の判断を迅速に行う必要があるため、月次の情報更新では遅いと考えられる。また、販売・生産計画の判断基準となる利益については、電機メーカーによくある柔軟に多品種対応できる組立工場の場合、限界利益[2]がより高くなる製品の組み合わせで固定費を賄って利益を拡大させることが大事であり、対象利益は限界利益、必要な原価情報は変動費となる。一方、取り扱い製品のライフサイクルが比較的長く、固定費の割合が高い装置産業であれば、月次情報で十分かもしれないが、投資効率が重視されるため、少ない稼働時間で多くの利益を生み出せる製品を捉える必要がある。したがって、判断基準となる利益は限界利益ではなく、貢献利益[3]が適しており、必要な原価情報は設備費や労務費を含めた個別固定費となる。
原価統制の意思決定を例に挙げると、個別受注生産の企業で、顧客仕様をもとに設計、五月雨出図[4]、製造を行っている場合、週次、日次で実績原価を捉え、見積原価と乖離するようであれば、設計の見直しなどを早期に対応する必要がある。一方、標準品を生産し製法も安定している見込生産の場合は、実際原価を原価構成要素ごとに捉えられれば、サイクルは月次でよいケースもある。
取り巻く内外環境が全く同じという企業は二つとなく、自社に必要な情報は何か、それを見定めることが大切である。
ただし、その前提には「原価情報そのものが正しいこと」がある。
精度の低い原価情報では意味がない
当然だが、必要なサイクル・単位・粒度で捉えられていたとしても、それら原価情報が実態と乖離していると意味がなく、誤った意思決定を招きかねない。しかしながら、実態に即した原価を捉えることは容易でないことも事実である。なぜなら、原材料費のように、製品との関係が明確な費用ばかりではないからである。
原価を製品別や工程別にどこまで見るべきか、見ることができるかは、企業によって異なる。しかし、間違いなく言えるのは、次のような例では意思決定を誤る可能性がある点である。
- AとBの2つの製品のうち、製品Aは製品Bに比べて段取り[5]に非常に手間のかかる製品だと現場は分かっているが、現行の原価計算方法では重量を基準に配賦しているため、製品Bよりも重量の軽い製品Aの方が低コストとなっている。
- ある工程に特に高額な設備Cを設置しているが、設備Cを使う製品と使わない製品で、作業時間が同じであれば同じコストとなっている。
- 同じ工場にあるDラインとEラインでは、使用設備の投資額は変わらないが、消費エネルギーは倍以上異なる。ところが、エネルギー費用を設備稼働時間で工場一律に配賦しているため、その差はコストに反映されていない。
上記例のように、自社の原価は実態に合っているだろうかという疑問が生じているようであれば、意思決定の情報として適切ではないといえ、精度向上のための取り組みが必要となる。
仕組みづくりにおいて留意すべきこと
「精度の高い生きた原価情報を管理統制し、利益拡大や資本効率向上に向けた最適な意思決定に活用する」ための仕組みづくりにおいて、以下3つの留意点についても触れておきたい。
1. 目的を念頭に、精度と運用負荷のバランスを考慮する
2. 原価管理の改革はトップダウンで着手する
3. グローバル原価管理においては原価計算の基本的な考え方を統一する
1. 目的を念頭に、精度と運用負荷のバランスを考慮する
原価情報を何のためにどのように使うのかという目的に照らし合わせたとき、非常に重要な原価情報であれば、運用負荷をかけてでも精度を上げることが求められるし、重要性がさほどでもないなら、運用負荷をかけてまで精度を上げる必要はない。一方で、原価情報の精度を上げたくても、運用が耐えられなければ意味がない。究極の精度を目指して高コスト体質になっては本末転倒である。大事なのはそのバランスの見極めだ。
例えば、製造指図ごとに実績工数を取れば精度は上がるかもしれないが、運用面で現実的ではない場合、実績工数を取らないまでも、BOM(Bills of materials:部品表)に設定されている標準工数を「みなし実績工数」として使用することが考えられる。または、製品の特性を表すもの(長さ、面積、重さなど)が手間とおおよその比例関係があるのであれば、それらを係数として使用することが考えられる。また、この製品は他製品より5割増しの手間がかかるといった現場の感覚値も、厳密な値ではなくとも妥当性があり、現行より実態にぐっと近づくのであれば使用に値する。0か100かではなく、50点より60点、60点より70点の原価計算方法を設定することがコツである。
2. 原価管理の改革はトップダウンで着手する
原価計算方法の見直しを図る時は、見直しの考え方を分かりやすく資料化し、何が何のために変わるのか共通理解を持っておくこと、そしてシミュレーションを行い、どこにどの程度のインパクトが生じるかを想定しておき、「腹決め」をしておくことが肝要である。
改革の目的が「意思決定に有益な情報を提供する」ことであり、「その精度が実態に近づくように取り組む」とプロジェクトスタート時には共有していたはずなのに、原価計算の方法を見直し、いざ生々しい数値が出てくると「これはまずい」「あれは現行の水準にしておかないと」という話が出てくることは決してまれではない。なぜなら、原価情報はさまざまな業務に関連しているため、原価の変更を受け入れられないという反応が生じるからである。一例で言うと、原価計算の方法を変えただけで、ある部門が扱っている製品の原価が上り、業績が押し下げられる、また別の部門では逆の現象が起きる。そうすると、業績への影響が小さくなるように、つまり、現行の原価に近い値となるように原価計算方法自体を調整しようとする動きが決まって出てくる。しかし、どれほど都合が悪かろうが、現行の原価より新たな計算方法による原価がより実態を表しているのであれば、それらを把握しなくてはならない。その上で、影響への対応策を別途考えればよいのである。
社内外への影響を含めて、全社として変化を受け入れるためにも経営層が関与することは不可欠である。
3. グローバル原価管理においては原価計算の基本的な考え方を統一する
グローバルに展開している各拠点の原価を管理統制する場合、拠点間の売買におけるグループ内利益を排除し、材料費、労務費、設備費といった原価構成要素ごとに捉えることが必要となる。そうすることで、各拠点の原価構造とその状態を適切に把握し、改善すべき拠点や最適生産地などの判断材料を得られるからである。この時、原価計算の方法による違いを生んではならない。例えば、特定製品について、国内と海外の複数工場での変動費を比較し、限界利益が最も高くなる最適な生産地を捉えようとしたとき、ある拠点では原材料費のみを変動費とし、ある拠点では直接労務費やエネルギー費用も変動費としていると、ベースが異なるため適切な判断ができなくなる。また、例えば、1時間あたりの加工費を表すレートの計算(費用÷総作業時間)において、保有時間(生産能力)を分母とするか、計画時間(予定稼働)を分母とするかといった方針も異なっていると、コスト競争力の比較が適切にできなくなってしまう。
グローバル原価管理だけでなく、複数工場を統括する場合にもいえることであるが、各工場での仕組みづくりの前に、原価計算の基本的な考え方をどのように統一するかを考えておかなければならない。これは、S&OP(Sales & Operations Planning:金額ベースで最適なSCMを実現すること)の前提としても、重要な要素である。
おわりに
多くの原価管理プロジェクトに携わり、精度と運用負荷のバランスは重要であると感じる一方で、それを管理レベルや意識を変えないことへの安易な言い訳にすべきではないとも筆者は考える。プロジェクトを推進していると、製品原価の1%に満たない数値を見るために負荷をかけるのは不毛であるという意見も挙がる。時としてその意見は妥当であるが、冒頭の自動車メーカーでは、小数点第2位(円単位)の世界で原価が管理統制されているのである。特に管理レベルの高い企業だからと片付けてしまってよいだろうか。
筆者は、原価管理レベルとコスト意識の低さが経営破たんを招いたケースに直面したことがある。その後、当該企業では、徹底した採算管理の仕組みが導入され、管理レベルを飛躍的に上げてV字回復に至った。そこで働く人たちとの会話を通じて何より驚かされたのは意識の変化であった。これまでの自分たちの当たり前の行動が、わずかであってもコストや利益にどのような影響を与えているのか。それらが見える化されたことにより、現場の行動が随所で変わったのである。どこまで管理レベルを上げるか、その判断は企業によって異なるが、原価管理の高度化は、より迅速で的確な意思決定を支えるだけでなく、意識改革にも大きく寄与することを最後に述べておきたい。
- [1] 標準原価=標準単価×標準数量、実績原価=標準単価×実績数量、実際原価=実際単価×実績数量
- [2] 売上から変動費(売上や生産量に比例して増減する費用)を引いた利益
- [3] 限界利益から各製品の個別固定費(製品の製造や販売にかかった直接労務費や設備費用など)を引いた利益で、各製品が貢献した利益を指す。また、組織や顧客などの利益貢献度を把握する場合は、組織個別の固定費(組織の活動でかかる費用)、顧客個別の固定費(顧客との取引関係でかかる費用)を限界利益から差し引く
- [4] 長納期の大型製品において、一度に製品全ての詳細設計を行わず、部分的な図面を断続的に出すこと
- [5] 製品を切り替える際の事前準備で、治工具のセットや機械装置の調整、製造前の作業内容確認や掃除などを指す